What is a Gas Sensor?
Essentially, gas sensors work based on the physical or chemical interactions between gases and the materials on the sensor surface. Whether it is the detection of harmful gas leaks in industrial production, the monitoring of gas safety in home environments, or even the analysis of respiratory gases in the medical field, gas sensors play an indispensable role. With the development of the Internet of Things and smart home technologies, the application scenarios of gas sensors are constantly expanding, and the requirements for their sensitivity, selectivity, and stability are increasingly high.
How a Gas Sensor Works?
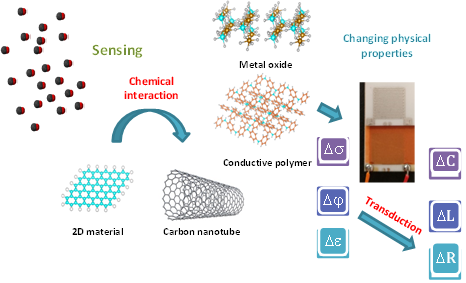
Semiconductor Gas Sensor Working Principle
infrared gas Sensors Working Principle
Another type is physical principle-based sensors, such as infrared gas sensors. A complete infrared gas sensor consists of an infrared light source, an optical chamber, an infrared detector, and signal conditioning circuitry. This type of sensor is made using the absorption of specific frequency infrared spectra by gases. Infrared light is emitted from the emitting end and directed towards the receiving end, and when there is gas present, it will absorb the infrared light, reducing the amount of light received, thereby detecting the gas content. Currently, the more advanced infrared sensors use dual-wavelength, dual-receiver to make the detection more accurate and reliable.
Electrochemical Gas Sensors Working Principle
There are also electrochemical gas sensors, whose working principle is: firstly, the substance of interest is reacted on the electrochemical electrode, producing an electrochemical reaction that converts the chemical change on the electrode into an electrical signal. This signal can be an electric current, potential difference, or resistance value, etc. Secondly, there is a reference electrode in the sensor that provides a reference potential to make the output signal of the electrochemical sensor more accurate and stable. Finally, the sensor's output signal is amplified through a signal amplification circuit and converted into a digital signal for processing by a computer.
Gas Sensor Construction
Labeled Diagram of Gas Sensor Internal Structure
The sensitive element is the core of the sensor, responsible for interacting with gas. For semiconductor gas sensors, the sensitive element is a metal oxide film coated on a ceramic tube or silicon substrate. There is usually a heating wire next to it, which is used to heat the sensitive material to a specific operating temperature (generally 200-400 & deg; C) to enhance its reaction activity with gas.
The function of the conversion circuit is to convert the physical or chemical changes (such as changes in resistance, current, and light intensity) generated by the sensitive element into standard electrical signals (such as voltage or current signals) for subsequent processing and analysis. This part usually includes electronic components such as resistors, capacitors, and operational amplifiers.
The housing not only protects the internal structure but also is designed with specific air holes to allow the target gas to enter and contact the sensitive element smoothly, while preventing the influence of interfering factors such as dust and water vapor. The housing material is usually plastic or metal, and its protection level varies according to the application scenario.
Auxiliary components may include temperature compensation elements. Because the characteristics of many sensitive materials are affected by temperature, temperature compensation can improve the measurement accuracy of the sensor. There are also lead terminals for connecting the sensor to external circuits.
Types of Gas Sensors Based on Sensing Principles
Semiconductor (Metal Oxide) Gas Sensors
These sensors rely on metal oxide materials (e.g., tin dioxide, tungsten oxide, zinc oxide) that react to specific gases. In clean air, oxygen molecules adhere to the material’s surface, trapping electrons and keeping resistance high (and current low). When target gases are present, they react with the oxygen, releasing electrons and reducing resistance—this change in resistance is measured to determine the gas concentration.
Advantages: Small size, low cost, fast response, and suitability for detecting methane, propane, carbon monoxide, etc.
Applications: Gas leak alarms, air purifiers, kitchen safety systems, and household detectors.Limitations: Lower precision compared to other types, making them ideal for daily use but not high-accuracy scenarios.
Electrochemical Gas Sensors
These sensors contain liquids or gels that react with specific gases, generating a weak electric current proportional to gas concentration—the higher the concentration, the stronger the current. They excel at both detecting and quantifying gases with high precision.Advantages: Compact, energy-efficient, stable results, and reliable for toxic gases like carbon monoxide, chlorine, or hydrogen sulfide.
Applications: Handheld detectors, safety helmets, indoor air monitors, medical diagnostics, and industrial safety tools.
Limitations: Limited lifespan (1–3 years) due to component aging, requiring replacement over time.
Infrared (IR/NDIR) Gas Sensors
Non-Dispersive Infrared (NDIR) sensors emit infrared light and measure how much is absorbed by gases & mdash; each gas has a unique absorption "fingerprint" for specific wavelengths. Reduced light intensity at the detector indicates gas presence and concentration.Advantages: No moving parts or chemical reactions, leading to long lifespan, high accuracy, and low maintenance.
Applications: Detecting carbon dioxide, methane, or refrigerants in heating systems, greenhouses, food storage, and ventilation controls.
Limitations: Larger size, higher cost, and susceptibility to dust/humidity interference.
Catalytic Bead Gas Sensors
These sensors use small, heated elements coated in a special mixture. When combustible gases contact the elements, surface reactions increase their temperature & mdash; this heat change is measured to estimate gas concentration.Advantages: Rugged, reliable for explosive gases, and widely used in heavy industry.
Applications: Refineries, chemical plants, and fuel handling facilities.
Limitations: Depend on oxygen to function and may miss certain gas types.
Photoionization Detectors (PID)
PIDs use intense ultraviolet light to ionize gas molecules into charged particles, generating a current that indicates gas presence. They excel at detecting trace volatile organic compounds (VOCs) like benzene or formaldehyde.Advantages: Fast response, high sensitivity to low concentrations.
Applications: Laboratories, hazardous waste sites, and portable field detectors.
Limitations: Not universal (misses some gases) and relatively expensive.
Photoacoustic Gas Sensors
Combining NDIR and acoustic technology, these sensors use pulsed light to heat gas molecules, creating pressure waves (sound) detected by microphones & mdash; signal strength correlates with gas concentration.Advantages: High sensitivity, non-contact measurement, long-term stability, and suitability for low gas levels.
Applications: Environmental monitoring, medical diagnostics, and continuous industrial safety systems.
Limitations: Sensitive to vibration/noise, complex calibration, and higher cost.
MEMS Gas Sensors
Micro-Electro-Mechanical Systems (MEMS) sensors integrate tiny mechanical/electronic components on silicon chips, using capacitive, thermal, or piezoelectric sensing. They are ultra-small and lightweight.Advantages: Low power consumption, easy integration into compact devices, and accurate for portable/wearable tech.
Applications: Smart electronics, automotive systems, drones, and industrial automation.
Limitations: Susceptible to environmental factors, limited measurement range, and shorter lifespan in harsh conditions.
Thermal Conductivity Gas Sensors
These measure how easily heat travels through air using a heated wire—gas presence alters heat conduction, which is measured to identify gas type.Advantages: Stable, no chemical reactions, suitable for inert gases like helium or argon.
Applications: Laboratories, cleanrooms, and gas filling stations.
Limitations: Less common for toxic or combustible gases, focusing mainly on gas composition analysis.
Each type balances accuracy, cost, size, and lifespan, making them suited to specific scenarios—from household safety to industrial precision monitoring.
Gas Sensor vs Carbon Monoxide Sensor
Aspect | Gas Sensor | Carbon Monoxide Sensor |
---|---|---|
Purpose | Detects a wide range of gases (depends on type). | Exclusively detects carbon monoxide (CO). |
Specificity | Non-specific (targets multiple gases). | Highly specific to CO. |
Technology | Varied (semiconductor, infrared, catalytic, etc.). | Mostly electrochemical (optimized for CO). |
Use Case Focus | Diverse (industrial, environmental, etc.). | Safety-critical for toxic CO exposure. |
Conclusion
Gas sensors enhance safety in various environments by detecting harmful gases. Understanding how they work and choosing the right sensor allows you to use them effectively at home, in the workplace, or anywhere clean air is a priority.
Hot-selling products of SIC
71421LA55J8 UPD44165184BF5-E40-EQ3-A SST39VF800A-70-4C-B3KE IS66WV1M16DBLL-55BLI-TR AS4C32M16SB-7BIN W25Q16FWSNIG
AS7C34098A-20JIN 752369-581-C W957D6HBCX7I TR IS61LPS12836EC-200B3LI MX25L12875FMI-10G QG82915PL
Product information is from SIC Electronics Limited. If you are interested in the product or need product parameters, you can contact us online at any time or send us an email: sales@sic-chip.com.
Gas sensor Frequently Asked Questions [FAQ]
1. Do gas sensors consume a lot of power?
It depends on the type. Electrochemical and catalytic sensors typically use very little power (milliamps), making them suitable for battery-powered devices like portable detectors. Infrared sensors, though, often need more power (sometimes watts) due to their light sources and complex electronics, so they’re better for wired setups.
2. Can gas sensors false alarm?
Yes, and it’s more common than you might think. Interfering gases are a big culprit—for example, a CO sensor might react to ethanol fumes. High humidity or sudden temperature spikes can also throw off readings. Choosing a sensor with built-in interference filtering helps, but no sensor is 100% immune.
3. How do gas sensors handle low concentrations of gas?
Sensitivity varies: some can detect gases in parts per billion (ppb) ranges (useful for environmental monitoring), while others only pick up parts per million (ppm) or higher (good for safety alarms). For example, formaldehyde sensors often need ppb-level sensitivity, while propane detectors focus on ppm to trigger alerts before ignition risks.
4. Are there gas sensors that work in explosive environments?
Absolutely—“intrinsically safe” sensors are designed for explosive atmospheres (like oil refineries or mines). They’re sealed to prevent sparks from the sensor itself from igniting flammable gases, and they meet strict safety standards (e.g., ATEX or UL Class I Div 1).
5. Can gas sensors be calibrated at home?
Probably not easily. Professional calibration requires access to precise, known concentrations of the target gas, which isn’t feasible for most users. Some manufacturers offer calibration kits for industrial sensors, but home users usually need to send the device back to the manufacturer or a service center.
6. Do gas sensors need to be cleaned?
Occasionally, yes. Dust, oil, or debris can block the sensor’s gas inlet, reducing responsiveness. Catalytic sensors, in particular, can get “poisoned” by silicones or lead fumes, which coat the sensing element. Gentle cleaning with compressed air (avoiding liquids) might help, but severe contamination often means replacing the sensor.
7. How fast do gas sensors respond to gas leaks?
Response time ranges from milliseconds to seconds. Catalytic sensors react quickly (under a second) to flammable gases, which is critical for safety. Electrochemical sensors might take 2–10 seconds to stabilize, while infrared sensors can be a bit slower (5–20 seconds) but more consistent.
8. Are there wireless gas sensors?
Yes, many modern sensors connect via Bluetooth, Wi-Fi, or LoRa for remote monitoring. They’re popular in smart homes (linking to apps for alerts) or industrial setups where wiring is tricky, like large warehouses. Battery life can be a trade-off, though—wireless features often drain power faster.
9. Can gas sensors detect gas through walls or barriers?
No, gases need to reach the sensor’s sensing element directly. Walls, sealed containers, or even thick plastic casings can block gas flow, leading to delayed or missed detections. Placement is key—sensors should be in open areas where gas is likely to accumulate, like near ceilings for lighter-than-air gases (methane) or floors for heavier ones (propane).
10. What happens if a gas sensor is exposed to gas levels way above its range?
It might “saturate”—the sensor can’t distinguish between very high concentrations, so readings max out. In extreme cases, high levels can damage the sensing element: for example, exposing a catalytic sensor to gas concentrations far exceeding its limit can burn out the catalyst, rendering it useless. That’s why many detectors include overload protection to shut down temporarily.